AWS Feed
Digitally Optimize your Factory Issue Resolution with Amazon Virtual Andon
As a manufacturing enterprise, maximizing your operational efficiency and optimizing output are critical in a competitive global market. Global black swan events such as COVID-19 have necessitated the ability to monitor remotely and respond to issues actively, on the factory floor.
Amazon Virtual Andon (AVA) is a digital notification system that helps factory personnel raise, route, track, and resolve factory floor issues more quickly. The solution was incubated in the Amazon Fulfillment Centers to monitor and resolve issues. It is now available as a self-deployable solution that manufacturers can use to optimize productivity.
An intuitive UI to deliver quick value
Amazon Virtual Andon comes with an intuitive user interface (UI) to set up your factory asset hierarchy, so you can model your real factory floor equipment (Figure 1). With AVA, you can create events (incidents) that are likely to occur across your factory. You can granularly tie events to the underlying stations and processes. Factory personnel can monitor manufacturing equipment for events, quickly raise issues, route the problem to specialized engineers, and ensure tracking and resolution of those issues.
Setup and configuration

Figure 1. Create your factory hierarchy
With AVA, you can set up your factory configuration quickly (see Figure 2a, 2b following). You can choose to create multiple factory sites, areas, stations, processes, and devices with the setup UI. You can also create users and assign them to Admin, Manager, Engineer, and Associate roles. You can set fine-grained controls on what users can access within the Permissions screen.
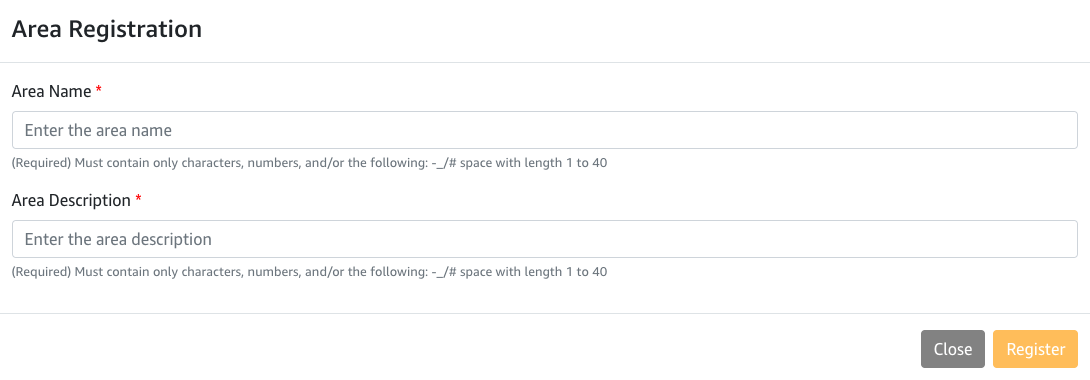
Figure 2a. Create new factory areas
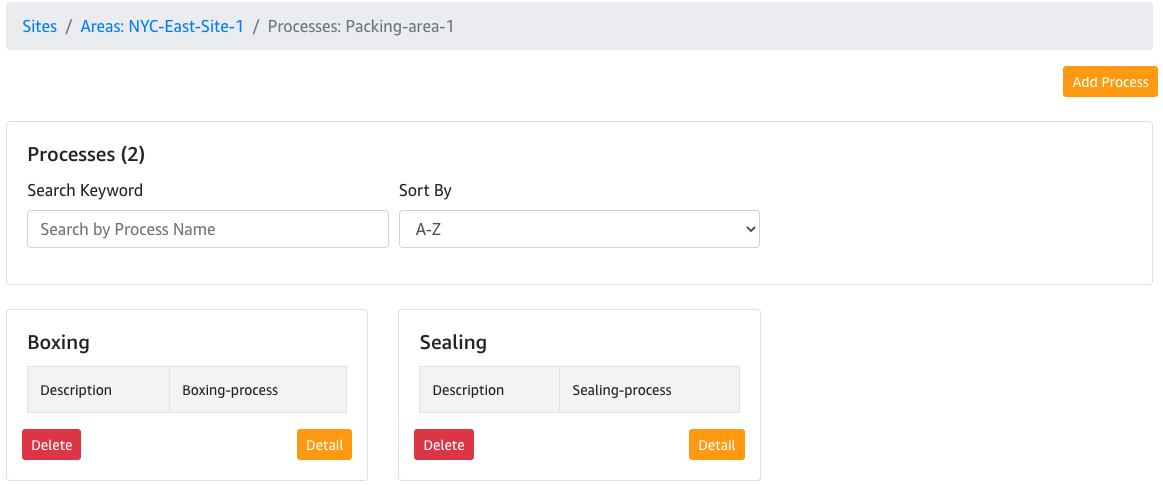
Figure 2b. Create factory processes
Client screen
In Figure 3, you can see AVA’s graphical client screen, where floor associates can raise issues when breakdowns occur. Associates can raise an issue by clicking on the issue tile. Once issues are raised, they are routed via Amazon Simple Notification Service (SNS) to subscribed emails addresses or phone numbers of specialized engineers for solving those specific breakdown events.
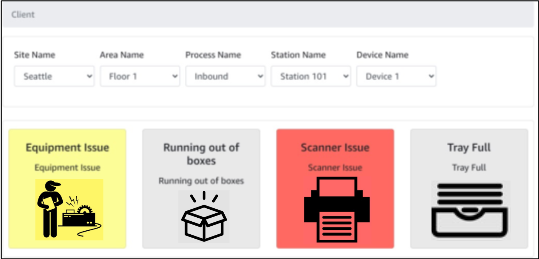
Figure 3. Raise issues screen
Observer screen
The issues routed to the engineers are visible on the observer screen, shown in Figure 4. The engineers can confirm that the problem is being addressed. This updates the status on the client screen, and allows for seamless communication between different users on the factory floor. The engineers can then close the issues by specifying a root cause and descriptive text. This enables prescriptive issue resolution, and can assist with future problems.
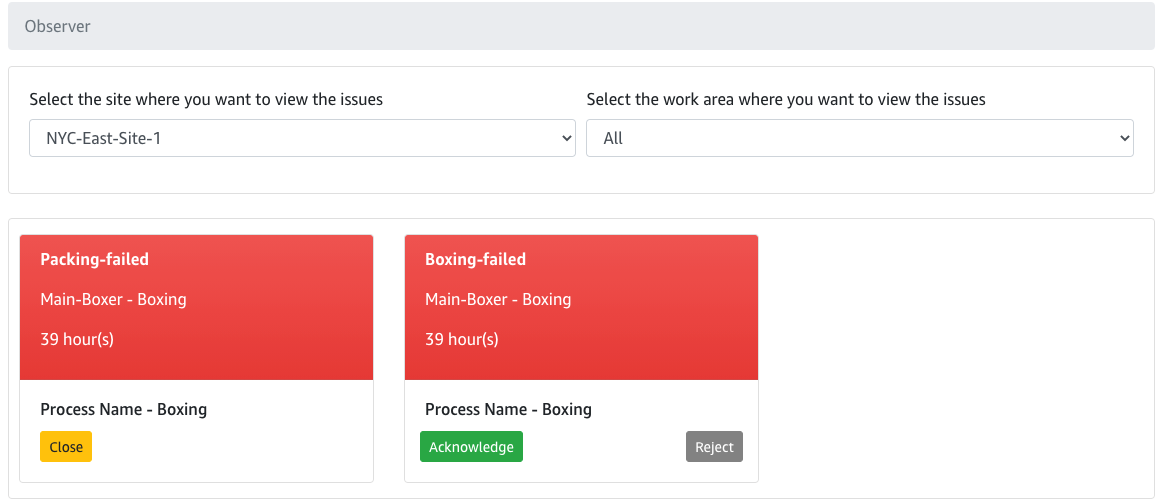
Figure 4. Issue response screen
Metrics reporting and API operations
AVA also provides robust reporting seen in Figure 5. This allows managers to view issue metrics for the selected sites and areas in the last seven days. The metric reporting will allow you to observe trends across different areas of your factory floor and optimize accordingly.
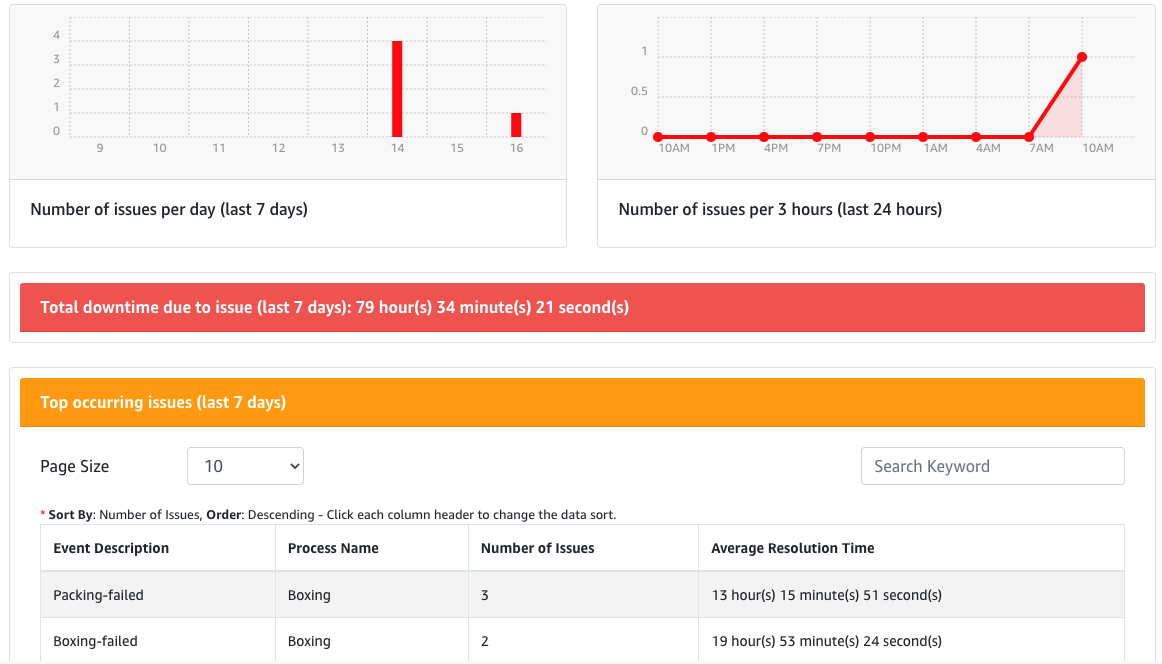
Figure 5. Metrics and reporting
Lastly, AVA comes with a rich set of GraphQL APIs that you can use to create sites, issues, and monitor and resolve problems programmatically. In addition, the APIs allow for custom integration with external systems such as factory MES (Manufacturing Execution System) systems, for automated issue creation and solving.
AVA deployment architecture
Deploying this solution with the default parameters builds the following environment in the AWS Cloud:
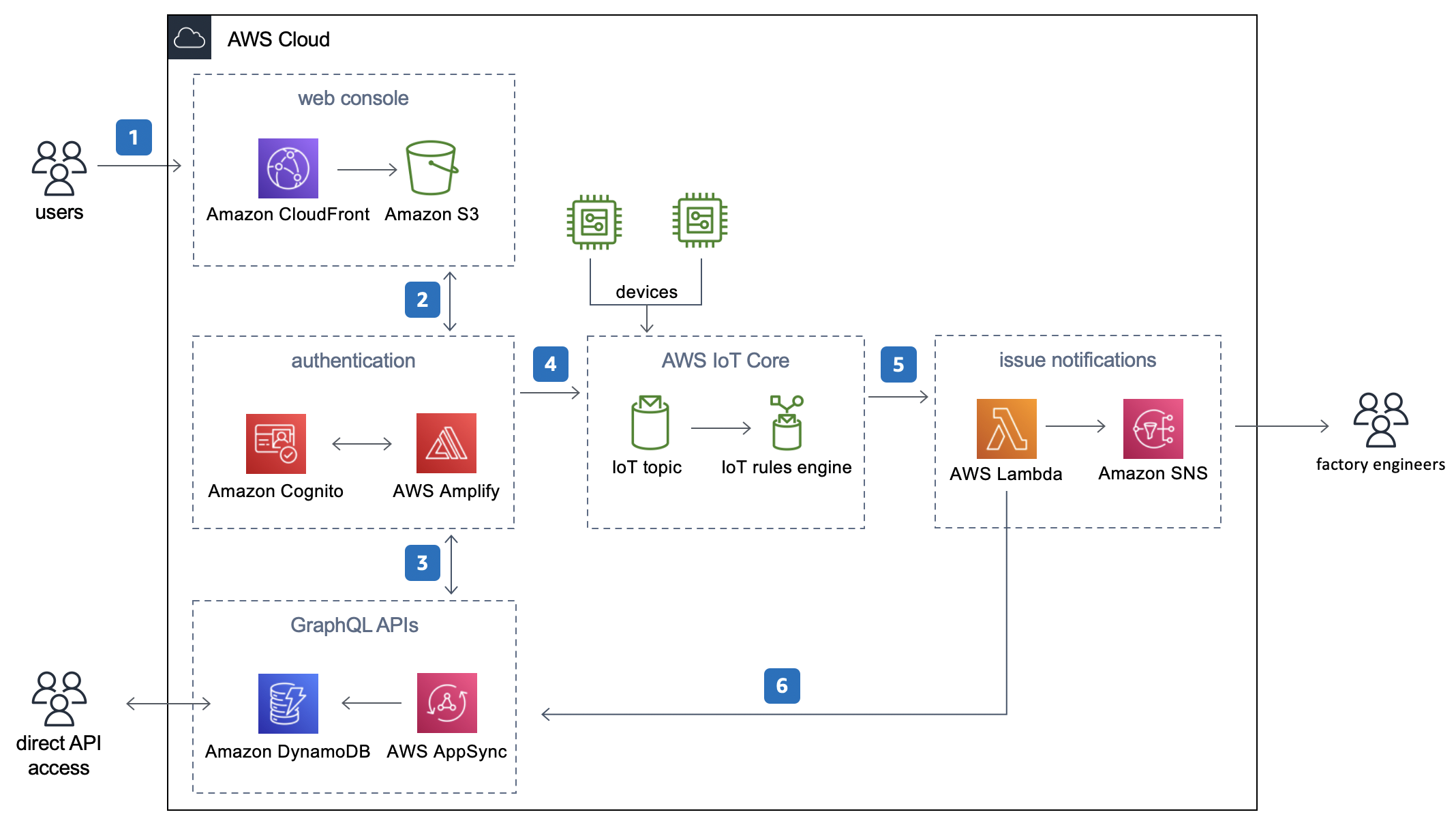
Figure 6. Amazon Virtual Andon deployment architecture
- An Amazon CloudFront web interface deploys into an Amazon Simple Storage Service (S3) bucket configured for web hosting.
- An Amazon Cognito user pool activates the solution’s administrators to register users and groups using the web interface.
- AWS AppSync GraphQL APIs and AWS Amplify power the web interface. Amazon DynamoDB tables store the factory data.
- An AWS IoT rules engine helps users monitor manufacturing workstations or devices for events. It then routes the events to the correct engineer for resolution in real time.
- Authorized users can interact with and receive notifications. Using an AWS Lambda function and Amazon SNS, you can send emails and SMS notifications.
- Issues created, acknowledged, and closed in the web interface are recorded and updated using AWS AppSync and DynamoDB.
Conclusion
Amazon Virtual Andon (AVA) is a self-deployable solution that helps you resolve factory floor issues more quickly and accurately. With AVA’s intuitive UI and open APIs, you can optimize issue resolution and focus on optimizing production output. You also can holistically monitor your manufacturing site remotely via an intuitive web application. Get started with Amazon Virtual Andon today.